Integration of Production Part Approval Process (PPAP) with Manufacturing Quality Management Data Threads Throughout the Supply Chain Can Help to Avoid Delays and Rejections in Aerospace, Automotive & Other Industries by Helping Manufacturers Document, Control, and Predict Better Quality
We all read the same news: In the aerospace sector, where a quality-related defect in a small part such as a bolt can have huge consequences. Because of the aerospace industry’s high visibility, the degree to which a manufactured part or component or assembly (“parts”) matches specifications has, for a host of reasons we will not delve into here, received greater attention from safety inspectors, the general public, and the news media than similar occurrences in other industries. Instead, we will explore some of the root causes behind those quality-related deficiencies and suggest some ways to address them.
Although instances in which parts do not meet quality standards appear to be rare occurrences, with global demand surges and the heavy potential cost of flight delays and accidents, manufacturers must address these hurdles to ensure quality and reliability.
Specifically, it is possible to improve upon the status quo by integrating Quality Assurance (QA), Quality Planning (QP), and Quality Control (QC) into a seamless and symbiotic approach.
Think of Quality as a formula for success:
- QA relates to how a process is performed or how a part is made to ensure zero defects,
- QP is the process of planning all the procedures that are necessary to ensure product quality before the part is made, and
- QC is the process of measuring and documenting manufacturing quality when the part is made.
Thrust for Change Can Create Lift
Some of these incidents may have multiple root causes beyond manufacturing quality, but one thing seems clear: The aerospace industry’s manufacturing quality-related challenges could be improved with the right systems in place.
For that reason, digital transformation is needed to unlock growth and efficiency and prevent manufacturing quality issues from occurring.
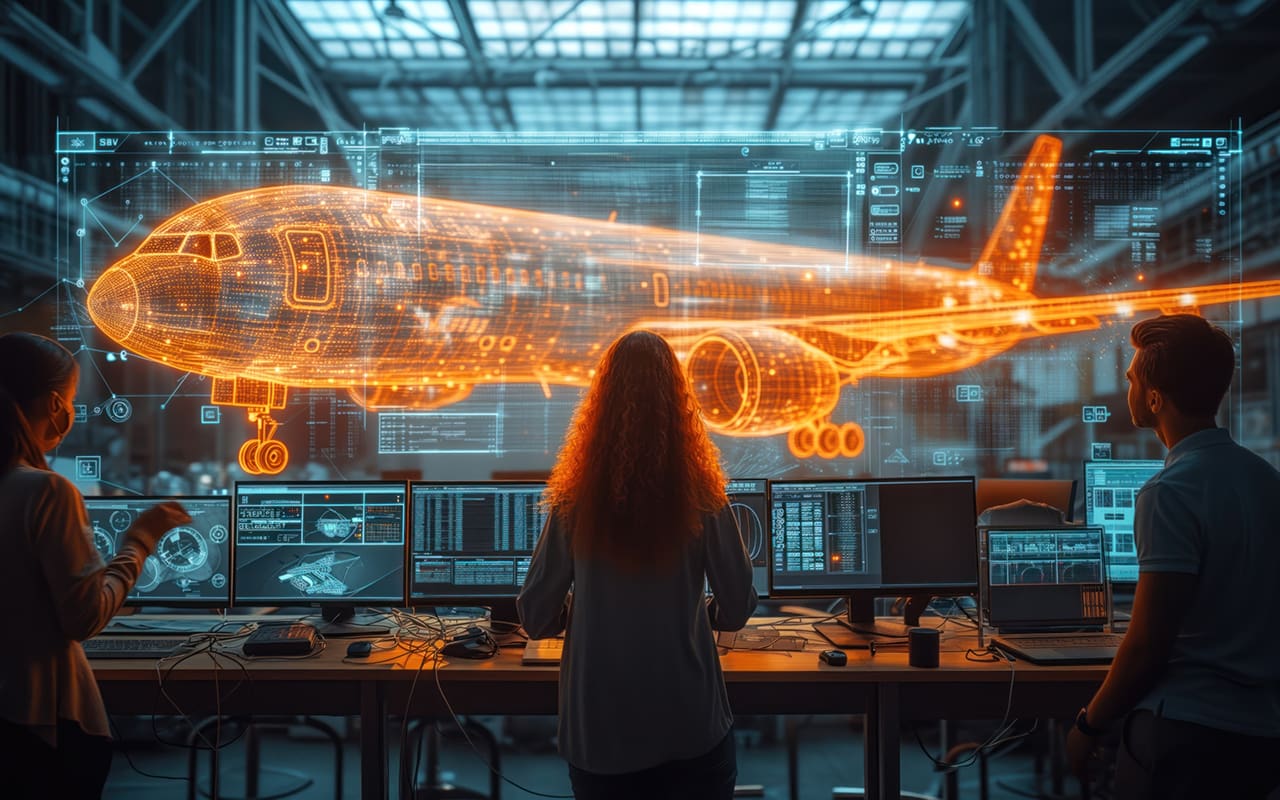
A Wide-Body Solution
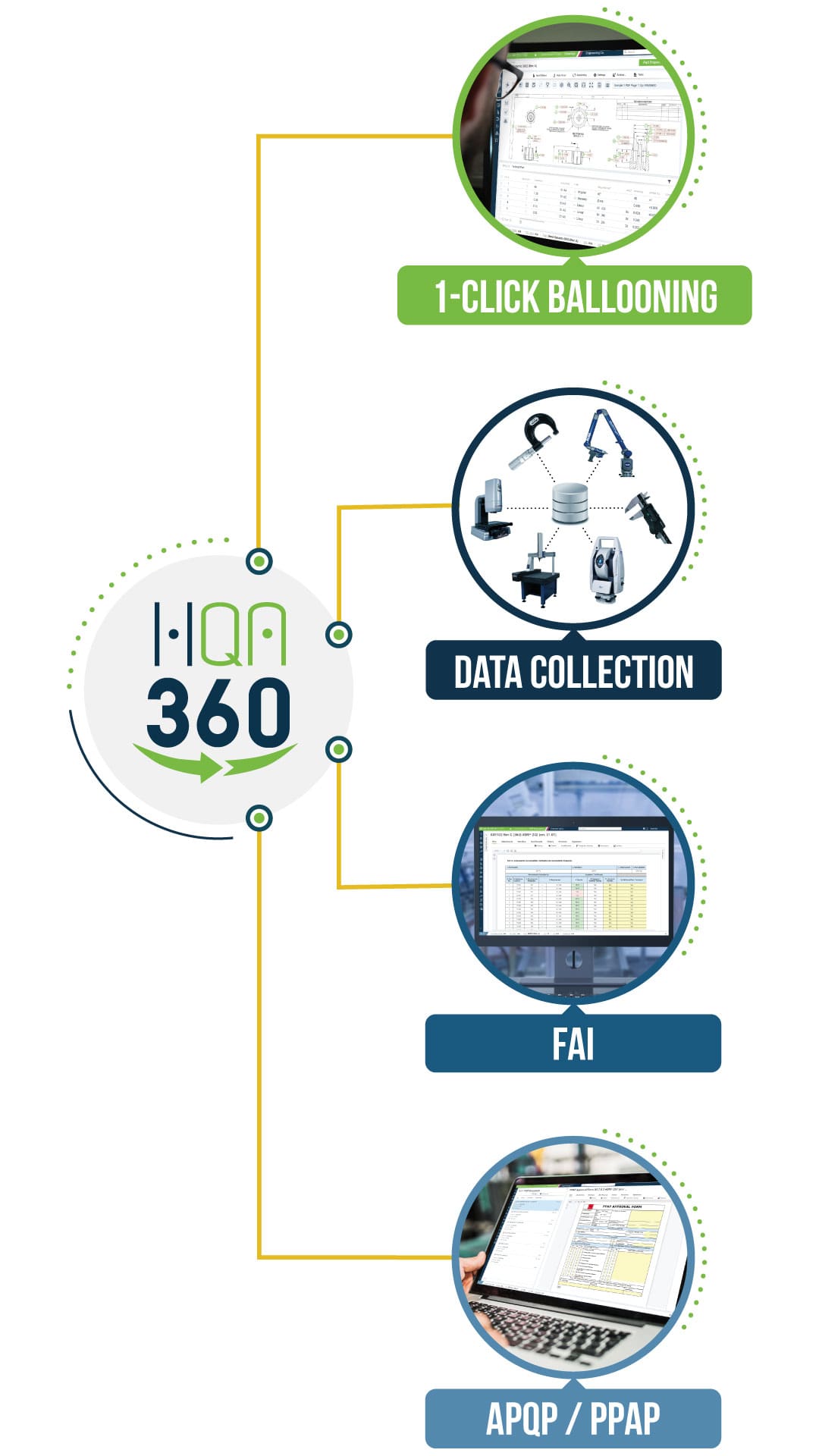