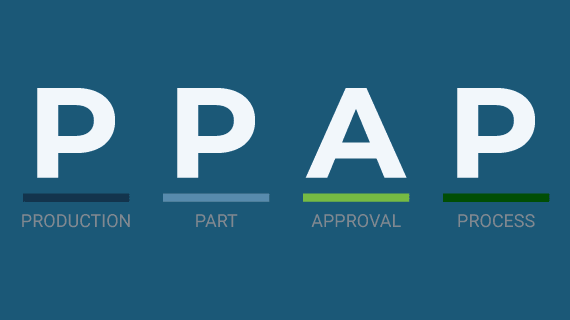
The primary purpose of PPAP is to provide evidence that an organization properly understands the specific requirements and the entire customer engineering design record.
It also demonstrates that the manufacturing process can produce products that consistently meet all engineering and quality requirements at the quoted production rate.
All Original Equipment Manufacturer (OEM) suppliers follow this standardized approach to hasten the approval of new and revised parts.
Overall, the PPAP process plays a significant role in improving equipment quality while at the same time lowering the time and expenses it takes in the part approval process.
What Does the PPAP Process Entail?
PPAP comprises 18 elements, but its application depends on customer requirements and the complexity of the parts undergoing manufacturing.
- Documenting the Design: This entails the technical drawings and purchase orders.
- Engineering Change Notice: It exists if there is a request for amendments to an existing part.
- Customer Approval: The customer’s engineering department must give approval.
- Design Failure Mode and Effects Analysis (FMEA): A detailed risk assessment that maps out possible loopholes in the design.
- Process Flow Diagram: The steps involved in production from start to finish.
- Process Failure Mode and Effects Analysis (PFMEA): Outlines possible failures within the manufacturing process.
- The Control Plan: Measures to mitigate possible failures.
- Measurement System Analysis: A record of the specifications and details of the equipment needed for the production process.
- Dimensional Layout Results: A validation check that ensures the technical drawings and the final product match.
- Design Verification Plan and Report: Validation records that include all relevant material certifications.
- Statistical Process Control (SPC): Statistical quality control documentation of the entire process and the components involved in making the final product.
- Qualified Laboratory Documentation: All the certifications from any lab testing.
- Appearance Removal Inspection: Approval of the product’s appearance by the customer.
- Sample Production Parts: The customer receives the product sample for approval.
- Master Sample: The final version of the product for which the customer must sign off.
- Checking Aids: All the necessary checks the manufacturer performs during production.
- Customer Specific Requirements: Refers to any specific requests the customer makes.
- Part Submission Warrant Form (PSW): A summary of everything captured in the PPAP submission, including declaration signatures.
Benefits of PPAP
While the PPAP comprises a long list of elements, it helps to ensure everything is produced according to the manufacturing plan. The process also helps users avoid the use of or distribution of unapproved parts.
It helps certify every crucial process needed to manufacture a part so it meets the engineering and manufacturing standards and quality specifications each time. It puts manufacturers in a position to provide quality output by ensuring they meet the requirements during the production run.
Suppliers
As a result, PPAP minimizes the risk of failure and enables users to take corrective actions promptly.
Customers
Overall, the process reduces the time and expenses used in the manufacturing process while strengthening the supplier and buyer relationship.
About High QA
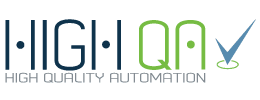
Our manufacturing quality management solution will help you save 75% of your time. Take your manufacturing from good-to-great with an all-in-one quality software solution.
Explore our website and discover what High QA can do for you and your suppliers. We are just a click away to answer questions or provide a demo of our software.