As a business expands, profit margins increase, and the need for additional staff and branches may become a reality. When that happens, it becomes a dream come true for every entrepreneur. However, a growing enterprise has its fair share of challenges, including the rigidity of the systems it is relying on. One such example is an Excel-based quality management system (QMS) that proves valuable when starting operations but unreliable when a company expands.
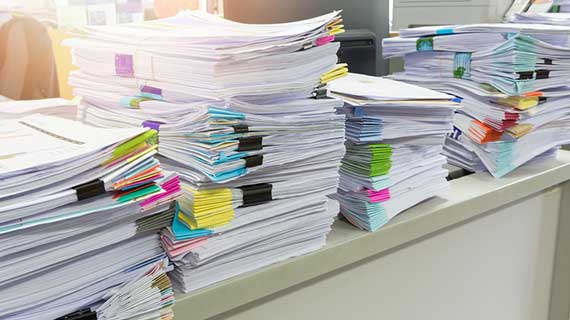
Here are a few signs that your Excel-based QMS is overstretched and can no longer afford you the peace that results from smooth operations.
1. Delays in Reporting
When it comes to quality management, speed is of the essence. You cannot afford to rely on an Excel-based QMS that is not responsive as your business grows because it denies you real-time visibility into your day-to-day activities.
Often, by the time you download an unformatted report from your system, cut and paste it into Excel, roll up the data, and then send each spreadsheet to the respective group, you are way past the deadline. And your Excel-based QMS is no longer reliable. The reason is that you end up assuming there are no underlying errors in your final report and that it ties out to what is in your source systems.
When that happens, decision-makers can hardly calculate spending, plan for the future, and make proactive decisions to improve quality management within your enterprise. It simply makes their work difficult.
An integrated QMS improves reporting. Standard forms and reports are available to all groups in the company and are based on the same data. That all leads to consistency, traceability and efficiency for manufactured parts.
2. Using Excel as a Data Warehouse
Using spreadsheets in the quality process is necessary. Often these spreadsheets have numerous columns and rows and even more tabs. They grow exponentially with each project. The adage old habits die hard is true. It is not unusual to discover that your facility relies on a particular file after several years while adding new cells and sheets to it without acknowledging the growth of such a file. That is a significant setback since a huge Excel file is prone to manual errors over and above being slow.
One wrong entry in a cell can yield inaccurate results. In turn, that will compromise the data you use for decision-making. Additionally, a massive Excel file can lead to data loss if the program crashes as you open the file. Although Excel is ideal for managing smaller data sets, relying on a single spreadsheet is not viable as your entity expands.
A centralized database in a QMS system provides a repository for all data used in a quality process. Drawings, forms, reports, regulations and approvals are in one location and are easily accessible for downstream processes and audits.
3. Quality Management Is Becoming a Time-Consuming Process
Using Microsoft Excel for quality management often requires several manual procedures, including downloading raw results from your system, cutting and pasting the data into a desirable format across multiple Excel files, rolling up the data, and updating formulas and links. You should also never forget to check for errors while you are at it. Phew! What a task.
The bottom line is that using Excel for quality management is a time-consuming manual process that is not worth your time and resources. Also, managing last-minute changes to Excel files is challenging, and you can easily forget to update formulas and links. Since management teams depend on authentic information, Excel-based QMS errors affect their confidence, which leads to misguided decisions that ultimately translate to inconsistencies, inefficiencies, and wasting of resources.
Current technology provides automation and optimization of previously manual processes. Comprehensive automation tools reduce costs, prevent human interpretation errors, improve delivery time and part quality ensuring your customers are always confident in your products.
4. Multiple Users Trying to Edit Spreadsheets Concurrently
If you use your Excel-based QMS in a team setting, only one person at a time can edit each file, and that is a major frustration that affects your operations in many ways. In that case, when an individual has such a file open, others will either have to wait or ask for a notification once it becomes available. That is such an inconvenience.
The other alternative, in this case, is saving a new version of that file and trying to merge the updates later. So, if one needs to wait for a colleague to edit an Excel file before handling other tasks, you will most probably realize reduced productivity. That can ultimately affect customer service and the reputation of your organization as well.
Conclusion
There you have it. Experiencing any of the signs above is evidence that your Excel-based QMS is no longer reliable and that your facility needs a better alternative. Using spreadsheets or paper as the basis of your quality system when your company expands is not viable because of the limitations you will encounter.
Just because you have always used manual spreadsheets in the past doesn’t mean you should use them today. Technology now provides opportunities to automate and optimize your manufacturing quality process. Take the steps today to move to an automated, integrated centralized database QMS and ensure your success for tomorrow.
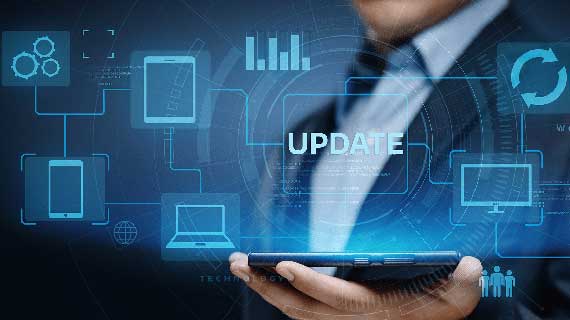